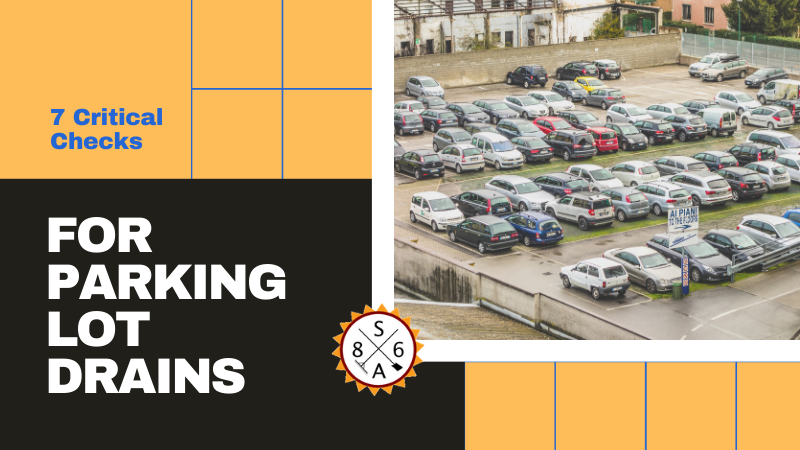
7 Critical Checks for Parking Lot Drains
Business owners commonly think about cracks and damage that lead to asphalt repair; however, it is just as important to think about parking lot drains as well because parking lot repair can be expensive. Water is a good thing when it comes to parking lots; however, too much water can also lead to serious damage. Even shallow puddles can cause the surface to become slippery. Cars can lose control and collide with other vehicles, leading to both personal injuries and property damage. This can cause the reputation of the business to suffer. This is where it is important to check parking lot drainage, starting with the drains themselves.
Checking for Parking Lot Drainage: The Drains
Some of the most important items that need to be on this checklist regarding parking lot drains include:
Water Collection: First, take a look around the drain. Make sure there isn’t any water ponding around the drain. If water starts to pool around the drain, it will collect along the sides. As a result, pressure around the drain will start to increase. During the winter, this water will freeze. When water freezes, it expands. This will cause the drain and concrete to crack, leading to damage.
Flush with the Surface: All parking lot drains need to be flush with the asphalt surface. If it is not, this is a major concern. If the drain is not flush with the asphalt, this can cause water to pool. It can also lead to flooding.
Ring Popping Up: Another potential issue that people might notice with their parking lot drains is that the ring is popping up a little bit. In this case, a small asphalt patch can fix the issue. Just make sure the patch is level. This will prevent a collar from forming that will stop the water from draining correctly.
Inside: Be sure to check inside the drain as well. Take the time to look for gunk, foul smells, and debris. If there is a clog inside the drain, this can also lead to a mosquito nest, which is a major nuisance. To look inside the drain, test the drain by pouring water into it. It should drain properly.
Blockage: Of course, it is also important to make sure that parking lot drains are not blocked by either debris of vegetation. If the drain is blocked, water cannot reach it properly. This will lead to flooding.
Loose Material: Sometimes, there is loose material that forms around the drain. This could be sand, gravel, or other materials. This is a major problem if the drain is near a major road. This aggregate can be brought in by runoff and heavy rain. Ensure this is not accumulating within t the drain.
Pooling: Finally, look at the center of the parking lot. Does the water pool in this location? Parking lots usually slope from one end to the other to help water drain. If water is pooling in the center, this means the center of the parking lot has dropped, causing water to pool and preventing it from draining properly. This will require a parking lot repair.
These are the most important elements when it comes to checking parking lot drains. This is important for making sure that all moisture drains properly. It will prevent property damage from arising down the line and save people money on asphalt repair.
Business owners commonly think about cracks and damage that lead to asphalt repair; however, it is just as important to think about parking lot drains as well because parking lot repair can be expensive. Water is a good thing when it comes to parking lots; however, too much water can also lead to serious damage. Even shallow puddles can cause the surface to become slippery. Cars can lose control and collide with other vehicles, leading to both personal injuries and property damage. This can cause the reputation of the business to suffer. This is where it is important to check parking lot drainage, starting with the drains themselves.
Checking for Parking Lot Drainage: The Drains
Some of the most important items that need to be on this checklist regarding parking lot drains include:
Water Collection: First, take a look around the drain. Make sure there isn’t any water ponding around the drain. If water starts to pool around the drain, it will collect along the sides. As a result, pressure around the drain will start to increase. During the winter, this water will freeze. When water freezes, it expands. This will cause the drain and concrete to crack, leading to damage.
Flush with the Surface: All parking lot drains need to be flush with the asphalt surface. If it is not, this is a major concern. If the drain is not flush with the asphalt, this can cause water to pool. It can also lead to flooding.
Ring Popping Up: Another potential issue that people might notice with their parking lot drains is that the ring is popping up a little bit. In this case, a small asphalt patch can fix the issue. Just make sure the patch is level. This will prevent a collar from forming that will stop the water from draining correctly.
Inside: Be sure to check inside the drain as well. Take the time to look for gunk, foul smells, and debris. If there is a clog inside the drain, this can also lead to a mosquito nest, which is a major nuisance. To look inside the drain, test the drain by pouring water into it. It should drain properly.
Blockage: Of course, it is also important to make sure that parking lot drains are not blocked by either debris of vegetation. If the drain is blocked, water cannot reach it properly. This will lead to flooding.
Loose Material: Sometimes, there is loose material that forms around the drain. This could be sand, gravel, or other materials. This is a major problem if the drain is near a major road. This aggregate can be brought in by runoff and heavy rain. Ensure this is not accumulating within t the drain.
Pooling: Finally, look at the center of the parking lot. Does the water pool in this location? Parking lots usually slope from one end to the other to help water drain. If water is pooling in the center, this means the center of the parking lot has dropped, causing water to pool and preventing it from draining properly. This will require a parking lot repair.
These are the most important elements when it comes to checking parking lot drains. This is important for making sure that all moisture drains properly. It will prevent property damage from arising down the line and save people money on asphalt repair.