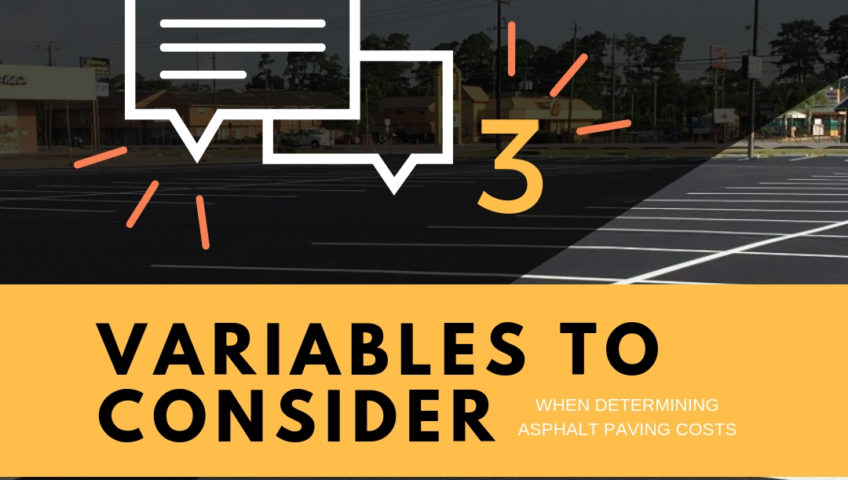
3 Variables To Consider When Determining Asphalt Paving Costs
Asphalt pavements are made from a mixture of stones, sand, and liquefied asphalt cement at 300°F. Upon cooling, the mixture forms a hard surface that is capable of accommodating heavy weights including vehicles. When computing asphalt paving costs, key among the factors to consider include soil, usage, and size. It is essential that you consult an experienced constructor to give you a quote before commencing on a project to ensure that your budget is capable of executing the task to completion.
Soil
The type of soil in the area to be paved plays a vital role in influencing asphalt paving costs. The kind of soil has a direct impact on the type of subgrade that will be used to support the load which will be transmitted from the pavement. The cost of paving increases with the increase in subgrade thickness. The subgrade is the working platform upon which the construction equipment is supported and is also the foundation to the pavement structure for supporting and distributing the traffic load. It is, therefore, critical to evaluate the how strong the subgrade should be before embarking on a pavement’s structural design. Failure to provide the required subgrade thickness can result in deflection rendering your work to be useless. Different soil types have to vary (texture) support capabilities which influence the depth of the subgrade. Soil texture is the average size of its mineral particles, and it defines how a type of soil can be used. Usually, most natural soils are made of different particle sizes which are used to distinguish one type from the other. Soils can be categorized into three main classes based on texture: Light, medium, and heavy-textured or fine grained. The three categories can further be classified as gravels, silts, sands, or clays.
Usage
The core function of an asphalt pavement is to distribute the weight on the wheels to the supporting subgrade. Asphalt paving costs vary with the type of load that will be accommodated on the pavement. Axle load can be classified into single, tandem, and multiple and can weigh up to 50,000 pounds. Asphalt pavements for use by tandem and multiple axle loads experience reduced load effects and thus, have a long lifespan. Asphalt pavements for use by single axle loads lack a diminished load effect and are thus, costly to pave due to the high-quality requirements to lengthen their lifespan. The volume and distribution of a load play a critical role in estimating the anticipated life of asphalt pavement and consequently, its cost. Usage of asphalt pavement can be predicted based on historical traffic records and truck percentage. To determine the effect of traffic, you require to establish the total volume of the two-way Average Daily Traffic (ADT). You can estimate a road’s ADT by use of a traffic map or a pneumatic tube on the road for some days. Traffic weight can have a dramatic effect on asphalt paving costs. Design differences have a direct impact on material, labor and equipment costs.
Size
The size of the area to be paved also impacts on the cost of asphalt paving. Size differences can be in parameters such as the gradient of the area to be paved, the extent of ground clearance required including the removal of physical barriers such as trees and buildings. Also, the cost of paving can be affected by whether the pavement will be flat or will have peaks and depressions to control the movement of storm water.
Asphalt pavements are made from a mixture of stones, sand, and liquefied asphalt cement at 300°F. Upon cooling, the mixture forms a hard surface that is capable of accommodating heavy weights including vehicles. When computing asphalt paving costs, key among the factors to consider include soil, usage, and size. It is essential that you consult an experienced constructor to give you a quote before commencing on a project to ensure that your budget is capable of executing the task to completion.
Soil
The type of soil in the area to be paved plays a vital role in influencing asphalt paving costs. The kind of soil has a direct impact on the type of subgrade that will be used to support the load which will be transmitted from the pavement. The cost of paving increases with the increase in subgrade thickness. The subgrade is the working platform upon which the construction equipment is supported and is also the foundation to the pavement structure for supporting and distributing the traffic load. It is, therefore, critical to evaluate the how strong the subgrade should be before embarking on a pavement’s structural design. Failure to provide the required subgrade thickness can result in deflection rendering your work to be useless. Different soil types have to vary (texture) support capabilities which influence the depth of the subgrade. Soil texture is the average size of its mineral particles, and it defines how a type of soil can be used. Usually, most natural soils are made of different particle sizes which are used to distinguish one type from the other. Soils can be categorized into three main classes based on texture: Light, medium, and heavy-textured or fine grained. The three categories can further be classified as gravels, silts, sands, or clays.
Usage
The core function of an asphalt pavement is to distribute the weight on the wheels to the supporting subgrade. Asphalt paving costs vary with the type of load that will be accommodated on the pavement. Axle load can be classified into single, tandem, and multiple and can weigh up to 50,000 pounds. Asphalt pavements for use by tandem and multiple axle loads experience reduced load effects and thus, have a long lifespan. Asphalt pavements for use by single axle loads lack a diminished load effect and are thus, costly to pave due to the high-quality requirements to lengthen their lifespan. The volume and distribution of a load play a critical role in estimating the anticipated life of asphalt pavement and consequently, its cost. Usage of asphalt pavement can be predicted based on historical traffic records and truck percentage. To determine the effect of traffic, you require to establish the total volume of the two-way Average Daily Traffic (ADT). You can estimate a road’s ADT by use of a traffic map or a pneumatic tube on the road for some days. Traffic weight can have a dramatic effect on asphalt paving costs. Design differences have a direct impact on material, labor and equipment costs.
Size
The size of the area to be paved also impacts on the cost of asphalt paving. Size differences can be in parameters such as the gradient of the area to be paved, the extent of ground clearance required including the removal of physical barriers such as trees and buildings. Also, the cost of paving can be affected by whether the pavement will be flat or will have peaks and depressions to control the movement of storm water.