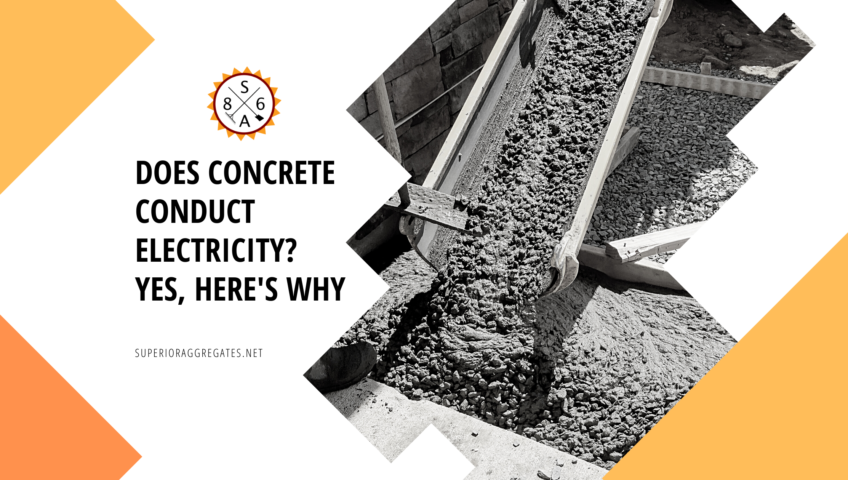
DOES CONCRETE CONDUCT ELECTRICITY? YES, HERE’S WHY
People generally don’t consider what conducts electricity, as long as they don’t suffer the results of the conductivity. People are aware that metals and even the ground move electricity. Concrete electricity, on the other hand, is outside the box for all but civil engineers, the military, and other such professionals. How does concrete move electrical currents?
What Is Concrete?
First, it’s important to understand how concrete is made. Many consider concrete and cement interchangeable. However, they are two completely different things. Cement is composed of crushed stone, shells, and other aggregate with chemical compositions of iron, calcium, and more. These things harden when combined with water to make cement.
Concrete is made when finely ground cement is added to things that have no chemical presence such as sand, gravel, and rocks. These act as a binder when mixed with water. It then hardens, forming concrete. How do these conduct electrical current?
How Does Concrete Conduct Electricity?
Completely dry concrete doesn’t conduct electricity; in fact, it insulates instead. When wet, concrete electricity has some verity, but not much. To conduct electricity, the ions in the elements of the cement have to be free to move.
That happens when the concrete is wet. The resistance of the concrete is conducive to the movement of these ions. Thus, on wet days, the ions move about with their electrical current in tow. The same is true of any wet material including wood.
How Can Concrete Become More Conducive?
To facilitate the movement of the ions more freely, something must be added to the concrete to make it more conducive. Since metal carries electrical current very well, adding steel and/or carbon fibers to the mix makes the concrete electrifying.
Would Concrete Electricity Be Attractive To Homeowners?
An overlay of conducive concrete is lighter than conventional concrete. Its electromagnetic properties protects smart homes’ connections as well as computers against hackers. Its warming properties use existing lines and is compatible with AC current in a 120 volt plug. It protects homes against lightning strikes.
Additionally, what homeowner doesn’t grumble when faced with shoveling the walkways and driveway in a snowy winter? Electrically charged concrete eliminates this chore. It removes the threat of deicing and salt products to the environment and wildlife. Walking across an electrically charged surface, though, won’t harm the walker.
There could be some benefit in conducive concrete due to its stability and bonding properties. In other words, storms won’t knock out the computers or other electronics. There will be no need for surge protection.
Final Thoughts
When people think of conducting electricity, they think of copper wires, aluminum buildings, and not swimming in a storm. Concrete never even crosses their consciousness.
However, it’s a great answer for homeowners seeking stable and conductive building materials. Its benefits to homeowners especially could save money and provide protection from Nature’s fury as well as from those with nefarious intent.