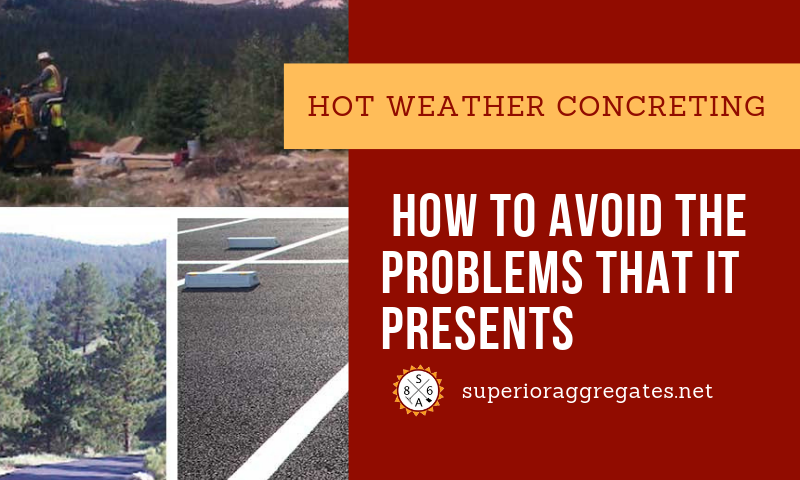
Hot Weather Concreting: How to Avoid the Problems that it Presents
The Perils of Concreting During
Hot Weather And How To Avoid Them
Hot weather concrete pouring can cause a myriad of problems. Many people think it is just about the heat itself but there is more to it than that. Many factors affect the quality and success of concreting during hot weather conditions. Hot weather, as defined by ACI 305R is any combination of the following:
- High ambient temperature above 90 degrees
- High concrete temperature
- Low relative humidity
- High wind speed
- Solar radiation
The heat is not the problem as concrete cures through hydration and not temperature. However, when the concrete becomes hotter than 77 degrees, it speeds up the hydration timing. If the concrete isn’t hydrated properly, it will be weak, crack easily and be more susceptible to damage from freezing and thawing. Construction crews must prepare for hot weather concrete placement.
Ways to Prepare for Pouring Concrete in “Hot Weather”
- Crews should avoid pouring the concrete during the hottest part of the day. Tracking hour by hour temps can assist with this determination. It is also wise to avoid extreme temperature changes. Pouring concrete on a hot day when followed by a cool night can cause thermal cracking to ensue.
- A team of workers should be available to ensure that the work is finished quickly and efficiently. Truck delivery should occur early in the day and a group of laborers ready to start immediately. Check for any potential delays so that the task will be completed in a timely manner.
- Sunshades, windbreaks or mist fogging can be used to protect and slow down the process of the concrete curing too quickly.
- Extended set additive, moderate heat cement and blended cements can provide solutions to pouring concrete in difficult conditions.
- Keeping concrete in the shade before pouring or using an evaporative retarder may help as well.
- Once the water is added to the mix, reduce the mixing time.
- Ice or cold water can be added to the mixture to cool down the concrete. Cold water can reduce the heat of the concrete by about 10 degrees and ice by approximately 20 degrees.
- If a slab is being poured, putting cool water on the sub-grade is another neat trick.
- Control-joints can be spaced closer together to aid in strengthening.
- Steel Fiber Concrete can be used to make slabs to add after walls and roofs are built out. Adding steel fiber to concrete has advantages and disadvantages so do your homework before choosing this method.
- Extreme weather conditions may require the infusion of liquid nitrogen into the mixers. This solution can be costly as there are concerns about damage to blades and precautions must be taken.
- There are several curing methods that can be used. Understanding these methods directly impacts how successful your curing process is. Concrete companies will want to have a plan ahead of time as to the correct method for each individual situation and to follow through with recommended procedures.
Setting concrete in difficult situations is a complicated process. However, with a little research and a lot of preparation, a concrete job can have favorable results.
The Perils of Concreting During
Hot Weather And How To Avoid Them
Hot weather concrete pouring can cause a myriad of problems. Many people think it is just about the heat itself but there is more to it than that. Many factors affect the quality and success of concreting during hot weather conditions. Hot weather, as defined by ACI 305R is any combination of the following:
- High ambient temperature above 90 degrees
- High concrete temperature
- Low relative humidity
- High wind speed
- Solar radiation
The heat is not the problem as concrete cures through hydration and not temperature. However, when the concrete becomes hotter than 77 degrees, it speeds up the hydration timing. If the concrete isn’t hydrated properly, it will be weak, crack easily and be more susceptible to damage from freezing and thawing. Construction crews must prepare for hot weather concrete placement.
Ways to Prepare for Pouring Concrete in “Hot Weather”
- Crews should avoid pouring the concrete during the hottest part of the day. Tracking hour by hour temps can assist with this determination. It is also wise to avoid extreme temperature changes. Pouring concrete on a hot day when followed by a cool night can cause thermal cracking to ensue.
- A team of workers should be available to ensure that the work is finished quickly and efficiently. Truck delivery should occur early in the day and a group of laborers ready to start immediately. Check for any potential delays so that the task will be completed in a timely manner.
- Sunshades, windbreaks or mist fogging can be used to protect and slow down the process of the concrete curing too quickly.
- Extended set additive, moderate heat cement and blended cements can provide solutions to pouring concrete in difficult conditions.
- Keeping concrete in the shade before pouring or using an evaporative retarder may help as well.
- Once the water is added to the mix, reduce the mixing time.
- Ice or cold water can be added to the mixture to cool down the concrete. Cold water can reduce the heat of the concrete by about 10 degrees and ice by approximately 20 degrees.
- If a slab is being poured, putting cool water on the sub-grade is another neat trick.
- Control-joints can be spaced closer together to aid in strengthening.
- Steel Fiber Concrete can be used to make slabs to add after walls and roofs are built out. Adding steel fiber to concrete has advantages and disadvantages so do your homework before choosing this method.
- Extreme weather conditions may require the infusion of liquid nitrogen into the mixers. This solution can be costly as there are concerns about damage to blades and precautions must be taken.
- There are several curing methods that can be used. Understanding these methods directly impacts how successful your curing process is. Concrete companies will want to have a plan ahead of time as to the correct method for each individual situation and to follow through with recommended procedures.